Tags: #buildingmaterials #buildingproducts #buildingscience #corrosion #fasteners #materialsscience #mgo #roguetesting
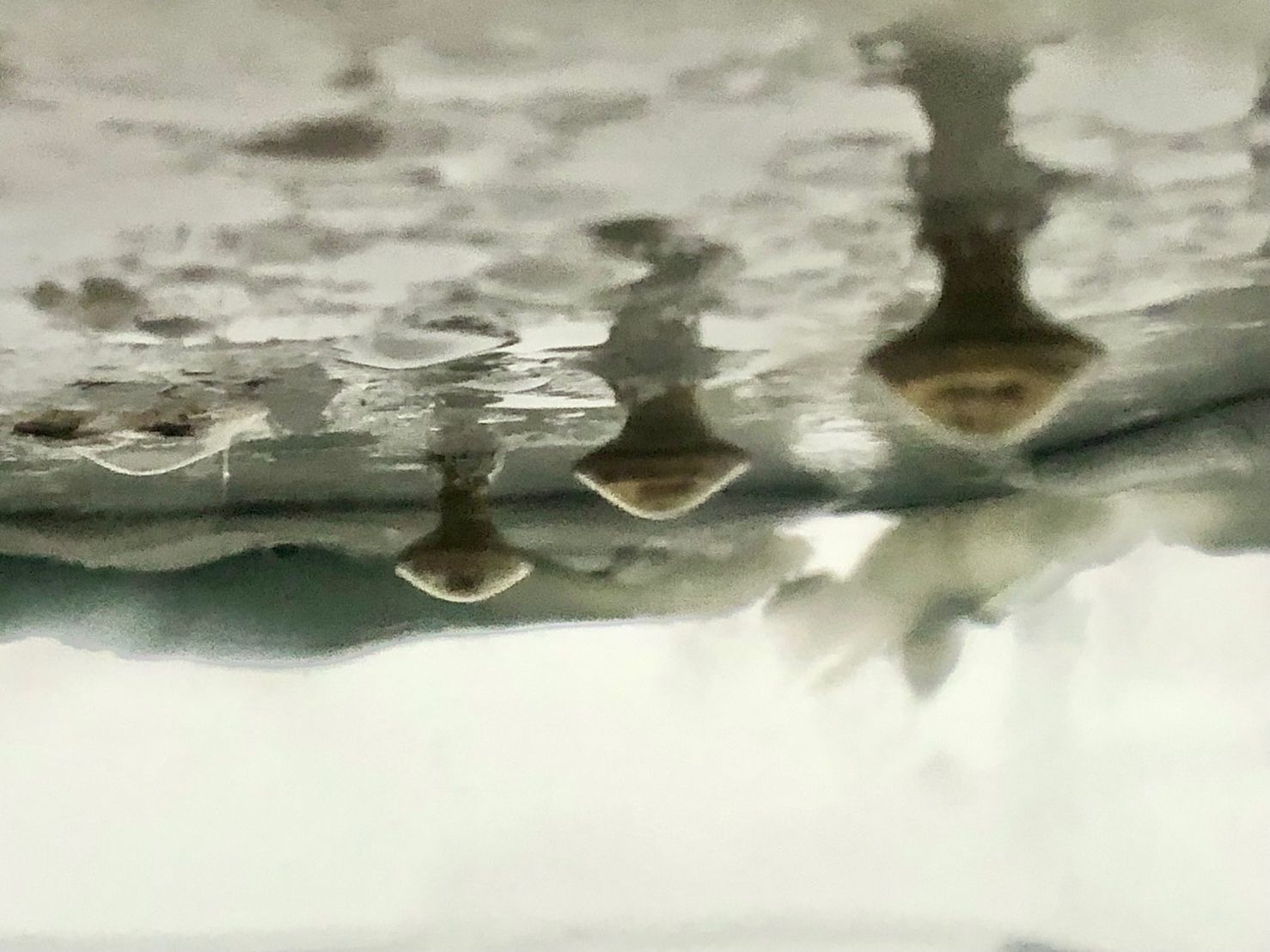
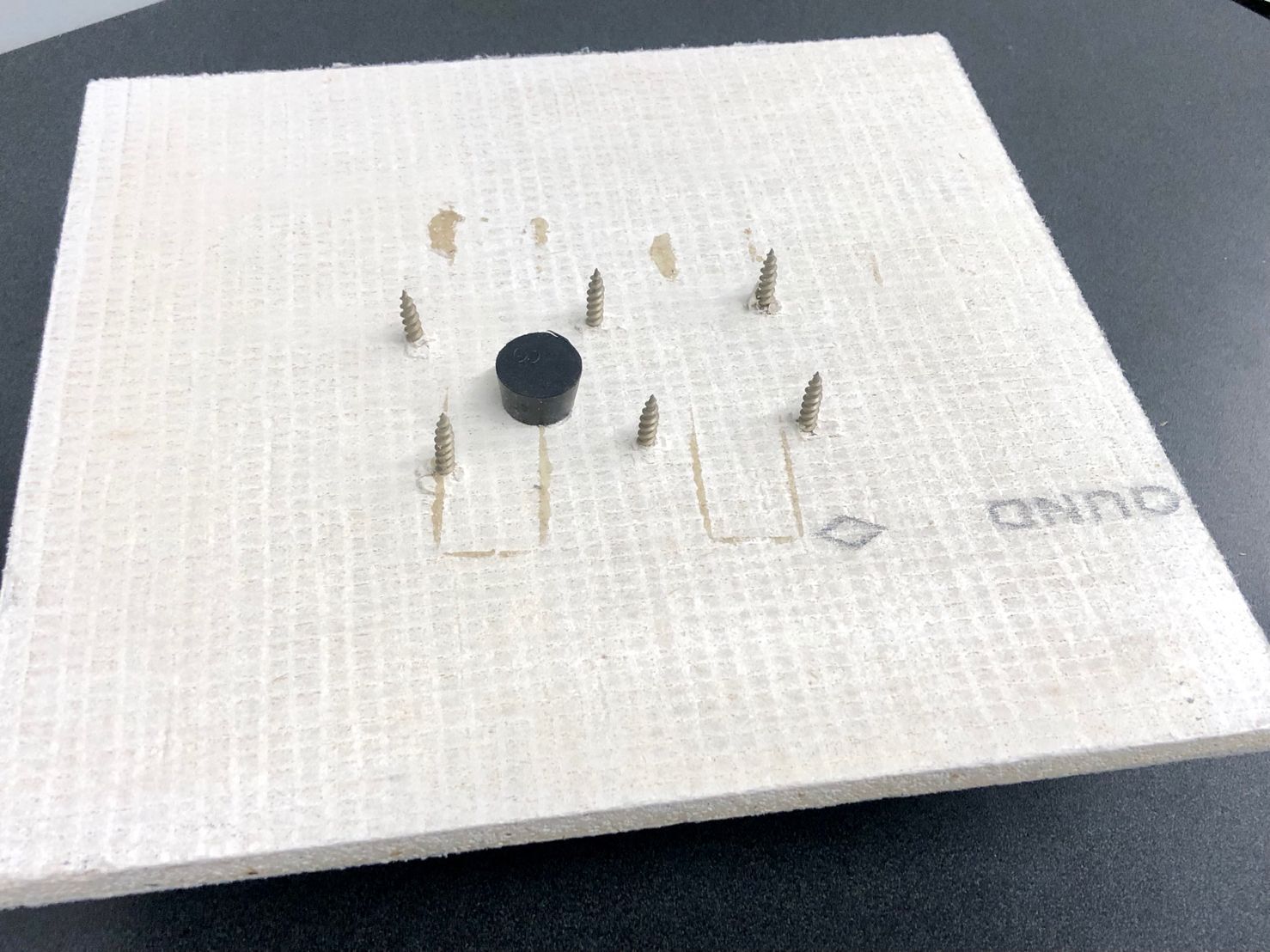
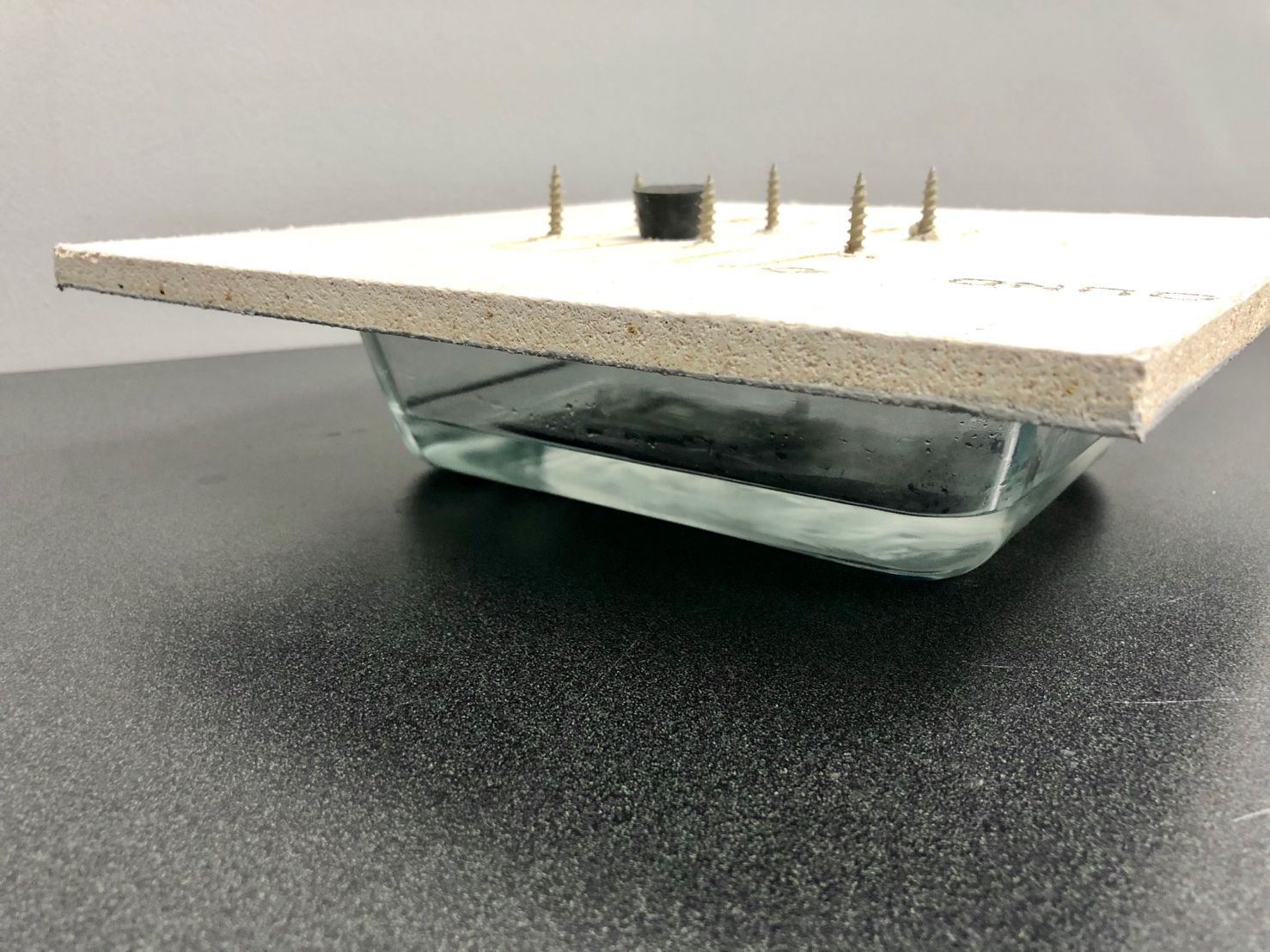
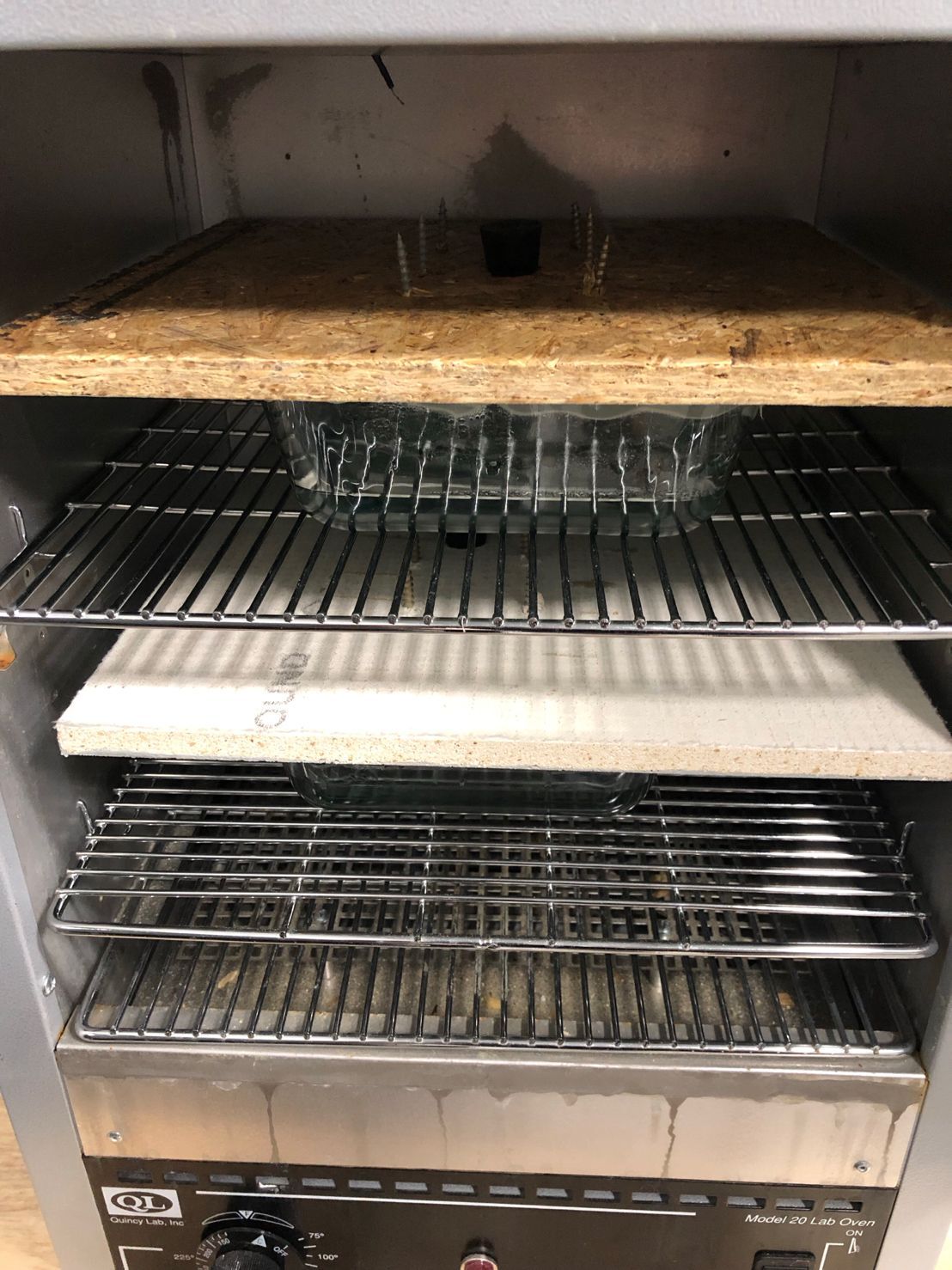
The perpetual rain machine: devising a simple test for fastener corrosion under temperature and substrate-dependence.
It’s generally agreed that rates of metal corrosion nearly double with each 10 degree increase in temperature. Increased temperatures are therefore advantageous not only in assessing risks but also for reducing test durations.
I’m currently working on a procedure that simplifies corrosion testing at high temperatures and high humidity – without expensive environmental chambers.
Fasteners are installed into the substrate, which may or may not include a WRB. Here, I show a coated MgO panel. The substrate is then inverted and sealed to a glass container that is partially filled with water. This forms a watertight, semi-closed chamber. The pre-tapped hole with accompanying stopper is used to replenish limited water loss due to vapor diffusion.
Relative humidity is maintained at 100% at a pre-defined temperature. Here, I’ve chosen 120F (49C) which is consistent with common corrosion testing protocols. At the chamber side, we see partial saturation where the dew point is reached. This water coalesces on raised fastener heads and panel interfaces until gravity takes hold, releasing it back to the pool below. The opposite (top) face is essentially dry.
It’s a Frankensteinian contraption. But one with a major advantage over conventional approaches. Aside from being simple, it creates two different humidity conditions at the same temperature. What happens at the WRB fastener interface (the water chamber side) is very different than what happens at the opposing face. Ultimately, a more realistic condition is achieved offering a continuum of conditions along the fastener’s shank.