Tags: #architecture #buildingenclosures #buildingenvelopes #buildingmaterials #buildingscience #flashings #materialsscience #mgo #tape
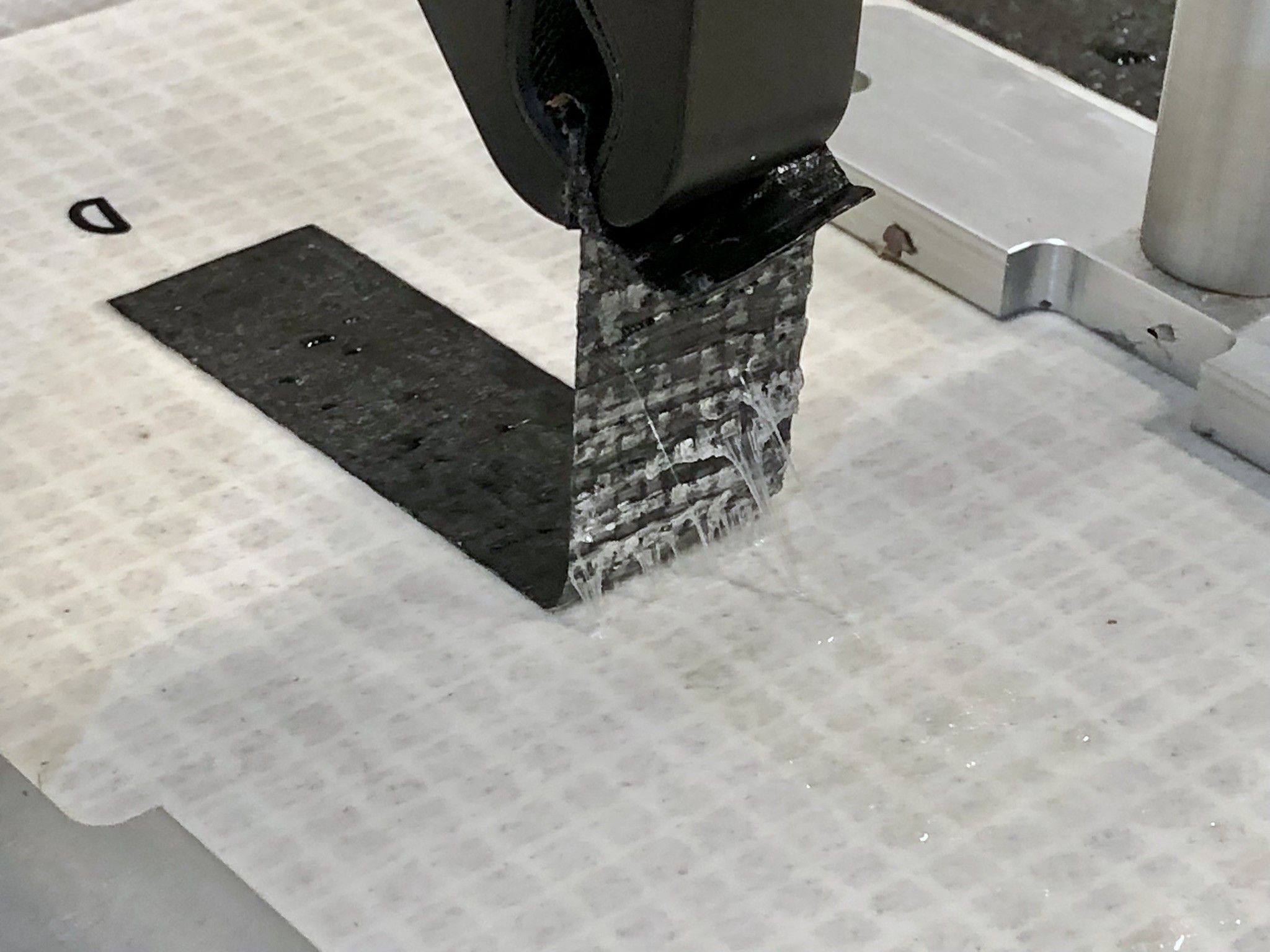
The benefits of using uncoated magnesium oxide in adhesion testing of self-adhered and liquid flashing.
Post-immersion adhesion testing per AAMA 711 and 714 is performed exclusively on anodized aluminum. Although this may make sense when considering fenestrations, it offers little insight when judging the efficacy on porous substrates where adhered interfaces may become wet or even saturated.
MgO is my go-to substrate when evaluating post-immersion adhesion on porous materials. Here’s why:
- It’s relevant. MgO is becoming a common substrate to which flashing products are applied. And it’s not always coated.
- MgO offers a smooth, uniform surface – one that is highly porous and conducive for most adhesives when dry.
- Uncoated MgO absorbs water, allowing adhered interfaces to be wetted.
- Unlike wood-based materials, MgO is dimensionally stable when exposed to water.
- MgO will not disintegrate in water.
- Consistent, reliable formulations of MgO are now available, offering common substrates for test comparisons.
- MgO is a keen differentiator of post-immersion adhesion and a good analog for porous materials in general.
- Test duration may be reduced from 7-days to 24 or 48 hours.
- Reduced immersion times are well-suited for cycling studies.
- Adhesion may be tested wet or at various stages of drying.