Tags: #architecture #buildingcodes #buildingenclosures #buildingenvelopes #buildingmaterials #buildingscience #EIFS #plastering

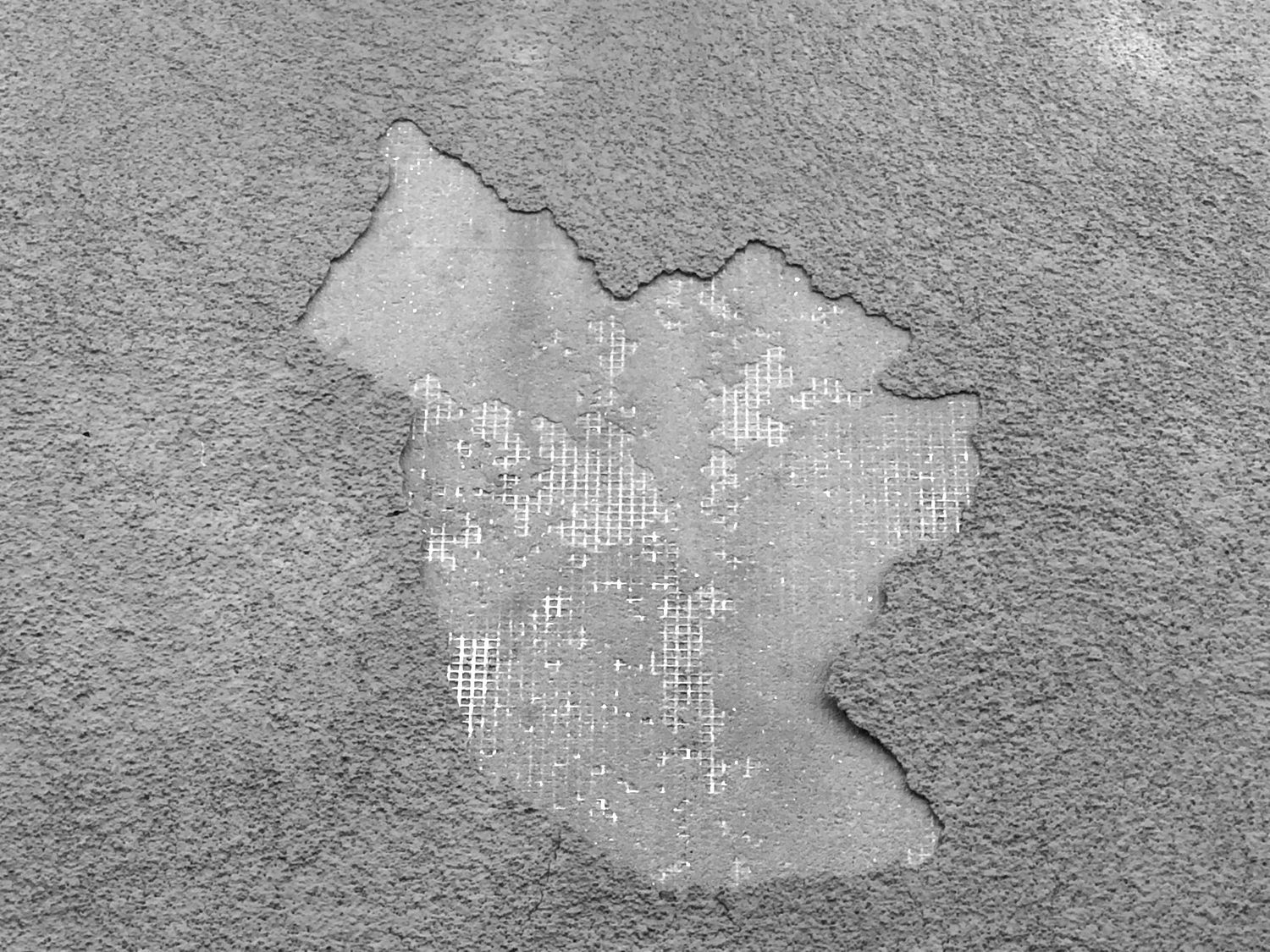
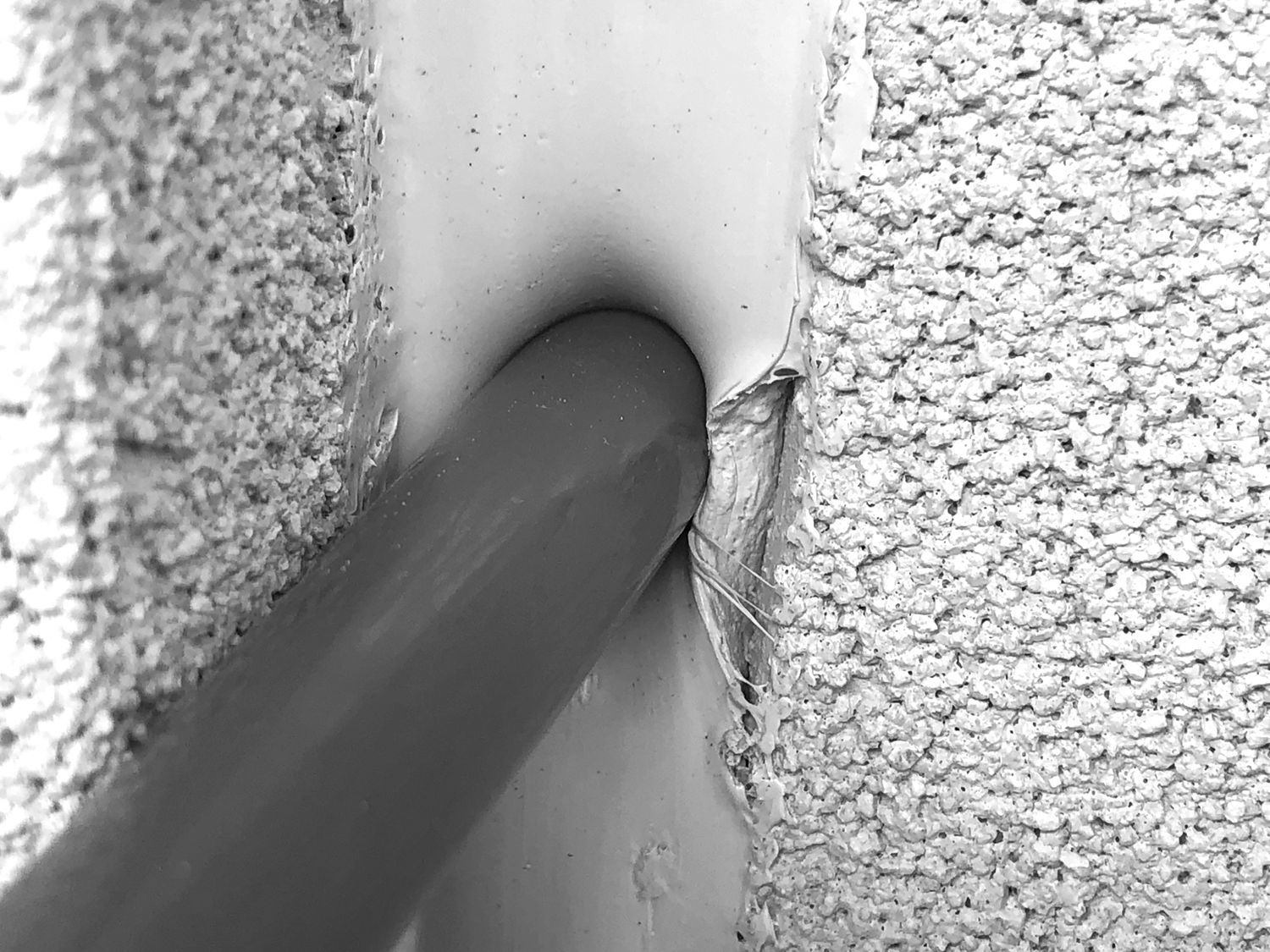
Several years ago, I wrote a blog article with the title “Open EIFS: A Resilient 100 Year Wall”. I meant it then, and I mean it now…. it’s easily achievable.
I plan to expand on that article in an upcoming white paper and a series of related posts. Here, I present five strategies that address most durability concerns. This list is directed largely towards owners, architects, and specifiers. Next week I’ll offer suggestions to EIFS manufacturers…. just in time for my impromptu attendance at EIMA 2023.
- Site inspections – Codes already require special inspections of EIFS. Excluded are drainable EIFS and EIFS over masonry and concrete. It’s 2023. All enclosure systems have gotten more complex, and all require stringent inspection, not just EIFS. Omit the exclusions. Inspect EIFS.
- Drainable EIFS – WRBs and the means for managing bulk water are requisite. And I prefer a substrate not made of wood. By the way, drainage is a misnomer. Think of it as a phase change space.
- Open EIFS – It means vapor open. It’s been 15 years since Oak Ridge’s study on the benefits of omitting cavity insulation and vapor barriers. Still, here we are designing aberrant hybrid walls having 30:70 ratios. A concern not unique to EIFS.
- Reinforcing mesh – Properly installed, high impact mesh vastly improves impact resistance, reduces cracking and prevents woodpecker damage. A tangible solution to a cornerstone argument in jurisdictional exclusions of EIFS.
- Sealants – They should have been part of warrantied EIFS systems since Day 1. It’s time we think of them in that way. Specify and test smartly. Know their limits and devise a robust maintenance plan.