Tags: #buildingdesign #buildingmaterials #buildingscience #insulation #materialsscience
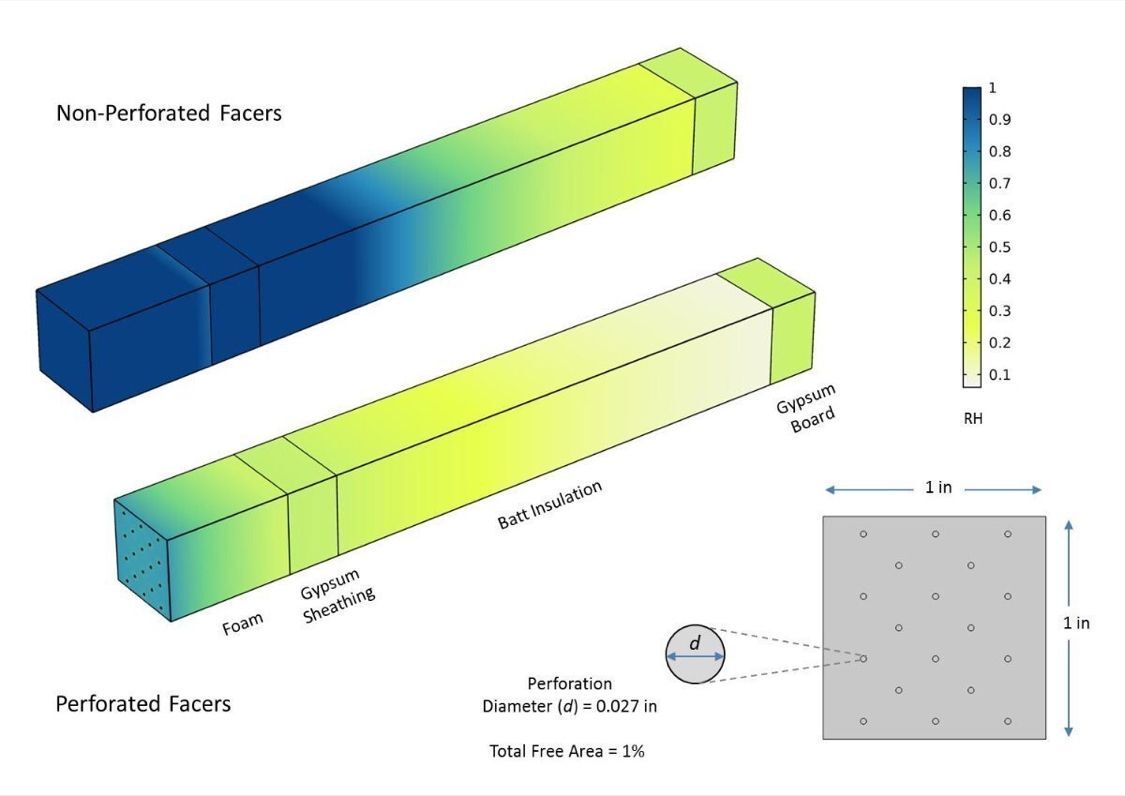
Facers are often distilled down to two varieties: permeable and impermeable. But there is a third, the perforated facer.
Facers serve many functions, from water and vapor management to product labeling, protection, and improved handling. Furthermore, their compositions can be optimized to achieve almost any desired attribute – the potential here is untapped.
I’ve posted this graphic in prior posts. It conveys a plot of relative humidity in hybrid wall assemblies. Each wall is configured with foam insulation having either non-perforated and perforated facers. The results show that a mere 1% perforated area can offer vastly improved performance. So when designing with code-minimum, prescriptive strategies, this approach deserves a second look.
While perforated facers should not serve as water-resistive barriers, they offer excellent substrates for tapes and flashings. So their role in air and thermal management is an important one. Other desired attributes such as product labeling, protection, and improved handing are preserved.